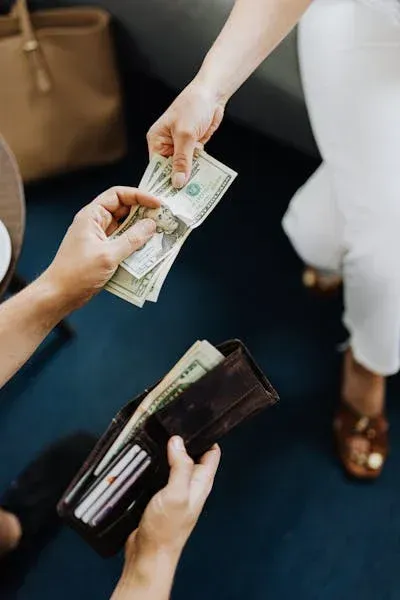
Top Factors That Affect Subdivision Paving Costs | All-Phase Asphalt
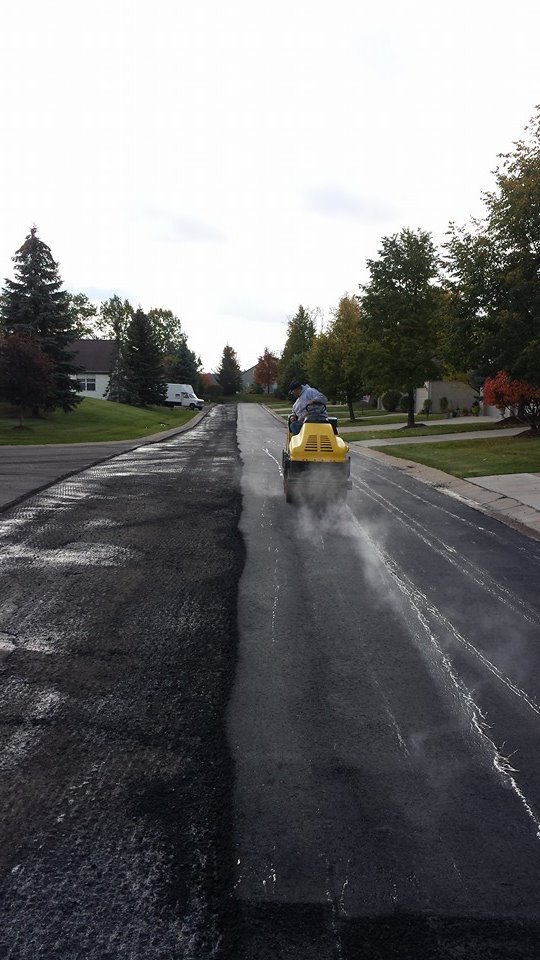
Subdivision Paving Costs: Key Factors You Need to Know
Subdivision paving costs vary based on several key factors. If you're a property developer, HOA, or city planner, understanding these factors helps you budget smarter and avoid surprises.
Everything from materials and labor to local regulations impacts the final price. Without a clear plan, costs can quickly add up.
This guide breaks down what drives subdivision paving costs, how to optimize your budget, and what to consider for long-term savings.
Key Factors That Influence Subdivision Paving Costs
Several factors determine how much it costs to pave a subdivision. The materials used, project size, labor, and even local regulations all affect the final price. Understanding these factors helps you make cost-effective decisions without sacrificing quality.
Material Selection & Quality
The type of paving material significantly impacts the overall cost. The two most common options are asphalt and concrete, each with its own price point and benefits.
Asphalt – More affordable upfront, easier to install, and ideal for colder climates. However, it requires routine maintenance like sealcoating and resurfacing.
Concrete – Costs more than asphalt but lasts longer with minimal maintenance. It’s a better option for areas with heavy traffic and extreme heat.
Other factors that affect material costs include:
✅ Recycled asphalt or eco-friendly options – Can reduce costs but may not last as long.
✅ Local availability – Materials sourced from far away increase transportation costs.
✅ Specialty mixes – Additives that improve durability or flexibility raise material prices.
Size & Scope of the Project
The larger the subdivision, the higher the cost—but bulk pricing can help reduce expenses.
Total square footage – More paving means higher costs, but large projects often get volume discounts on materials and labor.
Road width and additional infrastructure – Wider streets, sidewalks, curbs, and gutters increase costs.
Access and layout – If the site is hard to reach or has complex designs, expect higher labor and equipment costs.
Site Preparation & Land Conditions
Before paving starts, the ground must be cleared, graded, and stabilized. Some sites require minimal prep work, while others need extensive excavation, which adds to the total cost.
Poor soil conditions – Weak or unstable soil may need reinforcement or additional grading before paving.
Drainage issues – Installing proper drainage solutions prevents water damage but increases upfront costs.
Existing obstacles – Removing trees, rocks, or old pavement requires extra labor and equipment.
Skipping site prep may seem like a cost-saving move, but it leads to premature cracking, potholes, and costly repairs down the line.
Local Regulations & Permitting Costs
Local governments set zoning laws, building codes, and permitting requirements that affect subdivision paving costs. Failing to comply with these rules can lead to delays, fines, or expensive redesigns.
How Local Rules Impact Costs
Permits & Inspection Fees – Most municipalities require permits before paving begins. Fees vary based on location and project size. Some areas also charge for routine inspections.
Zoning & Land Use Regulations – Some cities enforce specific road widths, sidewalk requirements, and stormwater management rules, which increase material and labor costs.
Environmental & Drainage Compliance – Many local laws require stormwater management systems, such as retention ponds or pervious pavement, to prevent flooding and runoff issues. These add to the project’s cost but ensure long-term durability.
State & Local Taxes – Material and labor costs can be higher in some regions due to sales tax, transportation costs, and additional government fees.
How to Avoid Unnecessary Expenses
✅ Work with a contractor who understands local regulations to avoid compliance issues.
✅ Get permit estimates early so they don’t surprise you later.
✅ Plan for inspections and approvals to prevent delays in the paving schedule.
Ignoring local regulations can lead to costly do-overs. It’s better to follow the rules upfront than pay extra to fix mistakes later.
Labor & Equipment Costs
Subdivision paving is labor-intensive, requiring skilled workers and specialized equipment. The availability of labor and the type of machinery used directly impact overall costs.
What Affects Labor Costs?
Skilled vs. General Labor – Experienced paving crews charge more but work efficiently and deliver higher-quality results. Hiring inexperienced workers may save money initially but lead to errors and costly repairs.
Project Timeline – Rush jobs cost more because contractors may need to bring in extra workers or pay overtime. Planning ahead helps avoid unnecessary labor surcharges.
Seasonal Demand – Paving costs tend to be higher in peak seasons (spring and summer) due to increased demand. Scheduling your project during the off-season may result in lower labor costs.
Equipment & Machinery Costs
Paving requires heavy-duty machinery, and the cost depends on the type of equipment needed for the job.
Excavators & Graders – Used for land clearing and leveling. Sites with uneven terrain may require additional grading, increasing costs.
Asphalt Pavers & Concrete Mixers – Essential for laying pavement. High-quality equipment ensures a smoother, longer-lasting surface.
Compactors & Rollers – Used to compress materials and create a stable road surface. Insufficient compaction leads to weak pavement that deteriorates faster.
How to Manage Labor & Equipment Costs
✅ Hire a reputable contractor with experience in subdivision paving.
✅ Schedule work during the off-season to avoid peak pricing.
✅ Ensure proper project planning to prevent delays and extra labor charges.
Skipping on labor or equipment quality may seem like a cost-saving measure, but it often leads to poor results. Investing in the right team and tools ensures durability and fewer repairs down the line.
Drainage & Stormwater Management
Proper drainage is non-negotiable in subdivision paving. Without it, water can weaken the pavement, leading to cracks, potholes, and costly repairs. While adding drainage solutions increases upfront costs, it prevents expensive water damage in the future.
Why Drainage Matters in Subdivision Paving
Prevents Water Pooling – Standing water on roads causes erosion and surface deterioration.
Extends Pavement Lifespan – Proper drainage reduces freeze-thaw damage, a common issue in colder climates.
Complies with Regulations – Many cities require stormwater management systems to prevent flooding and environmental damage.
Drainage Solutions & Their Costs
Sloped Grading – Directs water away from the pavement naturally. More grading = higher costs, but it reduces the need for complex drainage systems.
Storm Drains & Catch Basins – Collect and redirect water to prevent pooling. These add upfront costs but are critical for long-term pavement stability.
Permeable Paving Options – Allows water to drain through the surface, reducing runoff. While more expensive initially, it can cut down on drainage system costs.
How to Optimize Drainage Costs
✅ Plan drainage solutions early to avoid expensive fixes after paving.
✅ Work with an experienced contractor to ensure proper grading and water flow.
✅ Balance upfront costs with long-term benefits—skimping on drainage leads to higher maintenance expenses later.
A well-designed drainage system protects your investment by keeping roads strong and stable for years.
Asphalt Thickness & Layering
The thickness of the asphalt layer plays a huge role in durability and cost. If the pavement is too thin, it won’t withstand heavy traffic and will need frequent repairs. On the other hand, using more asphalt than necessary increases costs without providing extra benefits.
How Asphalt Thickness Affects Cost & Longevity
Light Traffic Areas (e.g., residential streets) – Typically require 2 to 3 inches of asphalt.
Medium Traffic Areas (e.g., collector roads in subdivisions) – Usually need 4 to 5 inches to handle moderate vehicle loads.
Heavy Traffic Areas (e.g., main subdivision roads or roads used by trucks) – May require 6 inches or more, plus a reinforced base for added strength.
Base Layers & Why They Matter
A strong pavement starts with a solid foundation. The base layer provides stability and load-bearing support for the asphalt on top.
Aggregate Base (Gravel or Crushed Stone) – Helps with drainage and prevents shifting.
Subgrade Stabilization – Some sites need soil reinforcement before adding the base.
Multiple Asphalt Layers – Some roads use a base layer and a surface layer for extra durability.
How to Optimize Asphalt Thickness for Cost Savings
✅ Match thickness to traffic levels—don’t overpay for excessive layering.
✅ Invest in a strong base to prevent early cracking and repairs.
✅ Use high-quality asphalt mixes to improve longevity without unnecessary thickness.
Choosing the right asphalt thickness saves money in the long run by reducing the need for resurfacing and repairs.
Long-Term Maintenance & Lifecycle Costs
Paving a subdivision isn’t just about the initial installation—it’s about how well the pavement holds up over time. Proper maintenance extends the lifespan of the road, preventing expensive repairs and early replacements.
Key Maintenance Costs to Consider
Sealcoating – Protects asphalt from UV rays, moisture, and chemicals. Typically done every 3–5 years.
Crack Filling – Prevents small cracks from turning into potholes. Routine crack sealing reduces long-term damage.
Resurfacing – Adds a new asphalt layer over old pavement instead of full replacement. A cost-effective alternative to repaving.
Pothole Patching – Fixing potholes early prevents them from spreading. Neglecting them leads to costly reconstruction.
Why Regular Maintenance Lowers Long-Term Costs
Prevents Early Deterioration – Minor repairs cost much less than full replacements.
Reduces Liability Risks – Well-maintained roads lower the chances of vehicle damage claims and accidents.
Improves Curb Appeal & Property Value – Well-paved streets increase the desirability of a subdivision.
How to Minimize Lifecycle Costs
✅ Plan for routine maintenance instead of waiting for visible damage.
✅ Invest in high-quality materials upfront to reduce frequent repairs.
✅ Work with professionals who offer long-term pavement management solutions.
Ignoring maintenance leads to expensive repairs later. A smart maintenance strategy keeps roads in top shape without draining your budget.
How to Optimize Your Subdivision Paving Budget
Paving a subdivision is a major investment, but you don’t have to overspend to get quality, long-lasting results. Smart planning and the right choices can keep costs down without cutting corners.
1. Choose Cost-Effective Materials Without Sacrificing Durability
Standard asphalt is more budget-friendly than specialty mixes.
Recycled materials can lower costs while being eco-friendly.
Use the right asphalt thickness—too much increases costs, too little leads to early deterioration.
2. Partner with an Experienced Contractor
An expert paving team gets the job done efficiently, reducing wasted time and labor costs.
Contractors familiar with local regulations prevent costly permitting issues and delays.
Request multiple quotes to compare pricing, but don’t just pick the cheapest option—experience matters.
3. Plan for Long-Term Maintenance Instead of Just Installation Costs
Sealcoating, crack filling, and proper drainage save money over time.
Skipping maintenance leads to early repaving, which costs significantly more.
Set a budget for yearly upkeep to avoid unexpected expenses.
4. Time Your Project for Cost Savings
Paving during the off-season (fall or winter) can sometimes lead to lower labor costs.
Ordering materials in bulk for large projects can cut down per-unit pricing.
Plan ahead to avoid rush fees—tight deadlines often increase labor costs.
A well-planned paving project saves money upfront and in the long run. Investing in quality materials, expert contractors, and smart maintenance strategies keeps costs manageable while ensuring durable, high-quality roads.
Conclusion
For reliable, high-quality subdivision paving, trust All-Phase Asphalt to get the job done right. We specialize in paving services, parking lot repair, private road paving, sport court paving, lot milling, driveway paving, subdivision paving, and street paving. Our team delivers durable, long-lasting results using top-grade materials and expert craftsmanship.
Serving Seekonk, MA, Southeastern Massachusetts, and Rhode Island, we provide efficient, cost-effective solutions tailored to your project’s needs. Whether you're developing a new subdivision or maintaining existing roads, we ensure smooth, high-quality pavement built to last. Contact All-Phase Asphalt today for a consultation and get a free quote!